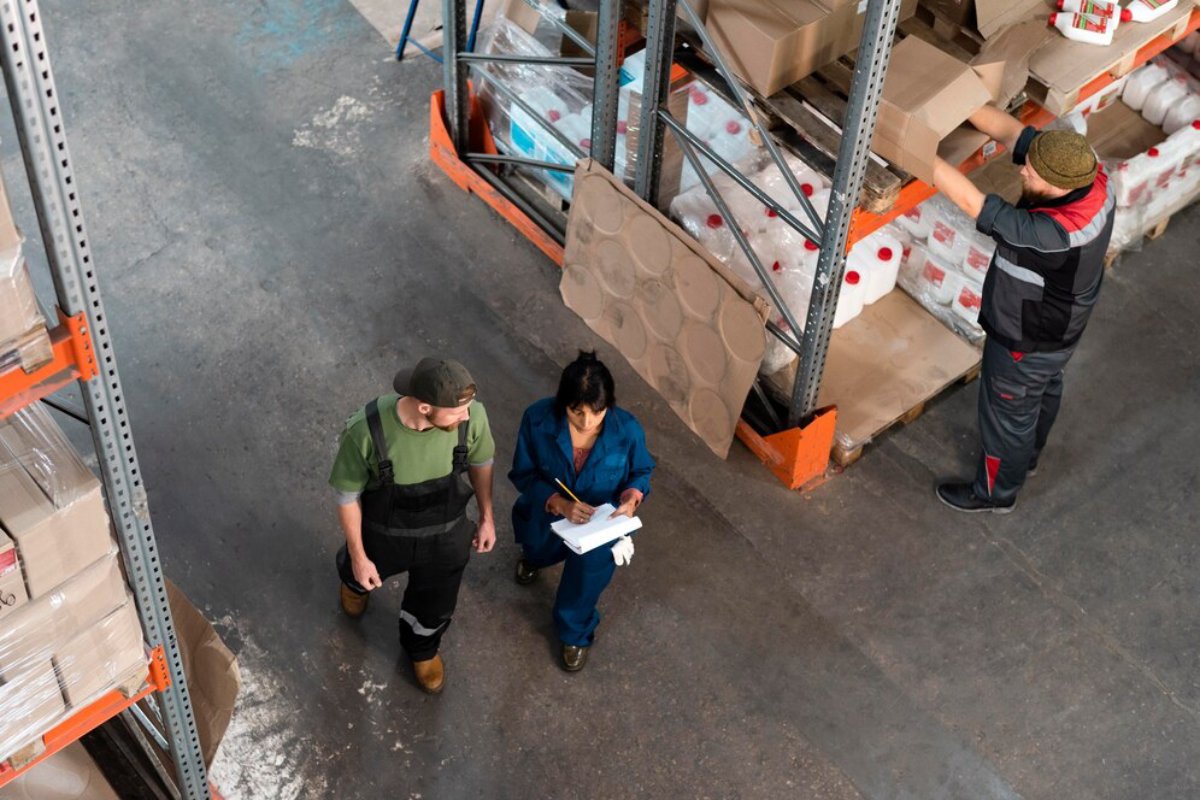
Warehouse Management: Best Practices for Retailers
Good warehouse management is key for retailers. It helps improve storage, boost order accuracy, and cut fulfilment costs. An optimised warehouse boosts productivity, minimises waste, and ensures faster delivery times. As eCommerce and omnichannel retail grow, retailers need to use best practices in warehouse management to stay competitive.
This guide offers key tips to improve warehouse efficiency, simplify inventory management, and boost logistics.
1. The Importance of Efficient Warehouse Management
a) Why Warehouse Management Matters
- Improved Order Accuracy: Minimizes shipping errors and returns.
- Faster Fulfillment: Reduces delays and enhances customer satisfaction.
- Optimised Storage Space: Maximizes warehouse capacity.
- Lower Operational Costs: Reduces unnecessary labour and inventory holding costs.
- Enhanced Inventory Control: Prevents overstocking and stockouts.
- Better Supplier Relationships: Good inventory management keeps strong ties with suppliers. It ensures timely orders and helps avoid last-minute stock shortages.
- Better Scalability: A good warehouse can quickly adjust to business growth, seasonal changes, and new market expansion.
b) Challenges in Warehouse Management
- Inefficient storage layout causing slow order picking.
- Poor inventory tracking, leading to lost or misplaced products.
- High fulfilment costs due to excessive labour and storage expenses.
- Delayed shipments affecting customer satisfaction.
- Difficulty managing multi-channel fulfillment.
- Adapting to changing customer expectations, such as faster delivery times and sustainable packaging.
- Managing workforce efficiency, including labour shortages and the need for skilled warehouse staff.
2. Warehouse Layout & Design for Maximum Efficiency
a) Optimize Warehouse Layout
- Design a flow-based layout to minimise unnecessary movement.
- Separate areas for receiving, storage, picking, packing, and shipping.
- Use a zoning system for high-demand and seasonal products.
- Implement wide aisles for smooth forklift and worker movement.
- Use color-coded sections and signage for quick navigation.
- Optimise dock areas to facilitate efficient loading and unloading.
b) Choose the Right Storage Solutions
- Use pallet racking systems for bulk storage.
- Implement bin shelving for small, fast-moving items.
- Adopt vertical storage solutions to maximise space.
- Invest in automated storage and retrieval systems (ASRS) for efficiency.
- Utilise modular shelving to allow for easy reconfiguration.
- Incorporate climate-controlled storage for temperature-sensitive goods.
c) Implement Slotting Optimization
- Place high-demand items closer to packing stations.
- Organise products based on sales velocity.
- Use data analytics to adjust storage locations dynamically.
- Implement ABC analysis to categorise inventory by value and movement speed.
- Regularly reassess and update slotting strategies to accommodate seasonal demand shifts.
3. Inventory Management Best Practices
a) Adopt Real-Time Inventory Tracking
- Implement RFID & barcode scanning to track inventory movement.
- Use cloud-based warehouse management systems (WMS).
- Conduct regular cycle counts to maintain accuracy.
- Integrate real-time tracking with supply chain partners for end-to-end visibility.
- Utilise mobile inventory tracking apps for on-the-go updates.
b) Reduce Overstocking & Stockouts
- Use demand forecasting tools to predict sales trends.
- Implement just-in-time (JIT) inventory systems.
- Set automated reorder points to avoid stock shortages.
- Establish safety stock levels for critical SKUs.
- Work closely with suppliers to maintain flexible replenishment schedules.
c) Optimize Returns Management
- Designate a dedicated returns processing area.
- Implement reverse logistics software.
- Offer resalable or refurbished options to minimise losses.
- Streamline the returns process with automated return labels and self-service portals.
- Analyse return trends to identify common issues and reduce future returns.
4. Streamlining Order Fulfillment Processes
a) Improve Picking & Packing Efficiency
- Use batch picking for high-volume orders.
- Implement pick-to-light and voice-picking technology.
- Pre-pack high-demand products to reduce fulfilment time.
- Optimise packaging materials to reduce weight and costs.
- Standardise packing procedures to minimise errors and improve efficiency.
b) Automate Warehouse Operations
- Utilise automated guided vehicles (AGVs) for material movement.
- Integrate robotic picking systems to speed up fulfilment.
- Implement AI-driven analytics to optimise workflow.
- Adopt conveyor belt systems to improve sorting and packing efficiency.
- Use automated labelling to reduce manual workload and improve accuracy.
c) Reduce Fulfillment Costs
- Negotiate better shipping rates with carriers.
- Consolidate orders to minimise shipping expenses.
- Use multi-warehouse fulfillment to reduce last-mile delivery costs.
- Optimise order batching to reduce travel time within the warehouse.
- Leverage dynamic pricing models for transportation and shipping.
5. Leveraging Technology for Warehouse Optimization
a) Warehouse Management Systems (WMS)
- Choose WMS software like SAP, Manhattan Associates, or NetSuite.
- Automate order routing and real-time inventory updates.
- Enable mobile access for warehouse workers.
- Integrate WMS with eCommerce platforms for seamless order processing.
- Utilise AI-driven WMS features to predict demand and suggest optimal stock levels.
b) Internet of Things (IoT) for Smart Warehousing
- Use IoT sensors to monitor warehouse conditions.
- Implement GPS tracking for shipment visibility.
- Analyse warehouse efficiency through predictive maintenance.
- Use smart shelving systems that notify when stock levels are low.
- Monitor worker productivity using IoT-enabled tracking devices.
c) AI & Machine Learning in Warehouse Management
- Use AI to predict optimal stock levels.
- Automate warehouse task scheduling for efficiency.
- Identify patterns to reduce storage and picking errors.
- Implement AI-powered demand forecasting to enhance supply chain responsiveness.
- Use machine learning algorithms to optimise storage slotting and minimise movement waste.
Conclusion
Effective warehouse management requires a smart plan. This plan should focus on storing inventory, fulfilling orders, and reducing costs. Retailers can increase productivity and make logistics easier. They can do this by using technology, improving warehouse layouts, and adding automation.
Investing in warehouse management best practices boosts efficiency. It also increases customer satisfaction and supports long-term business growth. Implement these strategies today to future-proof your retail supply chain!